Tuesday, November 26, 2024
Stannatech 2100 : Revolutionizing Immersion TIN Platingfor next-gen Performance
Immersion tin plating is a displacement reaction process where copper is dissolved during the deposition of tin, forming a tin layer directly on copper. This process creates a copper-tin intermetallic compound (IMC) that is crucial for soldering applications. Immersion tin layers are particularly attractive in the PCB market due to their robustness, long shelf life of at least 12 months, and absence of nickel, making them suitable for high-frequency applications. Additionally, immersion tin is more corrosion-resistant compared to other finishes, which is beneficial for automotive applications and offers a lower cost alternative to precious metal finishes.
Properties and Benefits of Stannatech 2100
The Stannatech 2100 immersion tin electrolyte introduces several enhancements over existing immersion tin solutions. Key benefits include:
- Reduced Viscosity: The new formulation significantly lowers the viscosity of the immersion tin solution, improving solution exchange and rinsing capabilities, especially in narrow features.
- Improved Soldering Performance: The Stannatech 2100 demonstrates better solder wetting characteristics, achieving lower spreading angles in solder spread tests compared to reference processes.
- Compatibility with Auxiliary Equipment: The process is designed to work seamlessly with existing auxiliary equipment, such as the constan and crystallizer, which help maintain consistent plating conditions and extend the bath life.
Typical Defects in Immersion Tin Plating
Despite its advantages, immersion tin plating can present certain risks and defects:
- Whisker Growth: Caused by the formation of intermetallics during aging, leading to stress and potential whisker formation.
- Copper Diffusion: The absence of a barrier layer allows copper to diffuse through the tin layer, limiting the shelf life of the finish.
- High Ionic Contamination: Poorly cured solder masks can absorb immersion tin chemistry, leading to high ionic contamination levels.
Key Improvements with Stannatech 2100
The Stannatech 2100 addresses several limitations of previous immersion tin processes:
- Enhanced Solution Exchange: The reduced viscosity allows for better solution exchange, preventing excessive copper dissolution and corrosion in narrow areas.
- Improved Rinsing: The lower viscosity facilitates easier rinsing, reducing drag-out of plating chemistry and minimizing ionic contamination.
- Lower Undercut Risk: The process shows a significant reduction in undercutting of solder masks, enhancing overall finish quality.
Soldering Performance Tests
Various soldering performance tests were conducted to evaluate the effectiveness of the Stannatech 2100:
- Solder Spread Test: Results indicated that the Stannatech 2100 achieved lower spreading angles, indicating better solder wetting compared to reference processes.
- Wetting Tests: The Stannatech 2100 consistently performed better in wetting tests, demonstrating superior solderability across different aging conditions.
- Dewetting Tests: The new process showed no failures in dewetting tests, indicating strong solder connections.
Root Causes of Soldering Defects
Common soldering defects associated with immersion tin can often be traced back to:
- Residues on Copper: Contaminants not removed before the tin plating can interfere with IMC growth and solder wetting.
- Inadequate Rinsing: Insufficient rinsing after the immersion tin process can leave residual chemistry that affects solderability.
- Volatile Contaminants: Volatiles from poorly cured solder masks can evaporate during reflow, leading to defects.
Post-Treatment Solutions
To further enhance the performance of immersion tin layers, several post-treatment solutions are available:
- Ionics 2100: Reduces ionic contamination, particularly important for automotive applications.
- Tin Post Treatment 8: Prevents yellowish discoloration of the immersion tin layer after reflow aging.
- Tin Post Treatment 2020: Strengthens the oxide layer, reducing the risk of dewetting defects.
Conclusion
The Stannatech 2100 immersion tin plating process represents a significant advancement in PCB manufacturing, addressing common challenges associated with traditional immersion tin methods. With its reduced viscosity, improved solderability, and compatibility with existing equipment, the Stannatech 2100 is poised to meet the evolving demands of the electronics industry, particularly in high-performance applications such as automotive and high-frequency devices.
As the industry continues to seek solutions that enhance reliability and performance, the Stannatech 2100 stands out as a promising option for next-generation immersion tin plating.
We at ESS ESS TRADING provide complete service and supply of chemicals in India . Contact us : Email: info@essesstrading.in Mobile: 9843019701
Friday, November 15, 2024
New Development in EN Corrosion Protection
This blog post discusses the latest developments in high phosphorus electroless nickel coatings, focusing on their superior corrosion protection capabilities compared to traditional methods. It covers the importance of coating thickness, the impact of porosity, and the evaluation methods used to assess corrosion resistance.
For more details and purchase mks Atotech Products
Contact us -Email: info@essesstrading.in Mobile: 9843019701
In a recent webinar, experts presented significant advancements in high phosphorus electroless nickel (EN) coatings aimed at improving corrosion protection. This post summarizes the key points discussed, including the importance of corrosion protection, the evaluation methods for coatings, and a comparison of new processes against existing technologies.
Understanding Corrosion Protection
Corrosion protection is crucial for extending the lifespan of components exposed to harsh environments. Electroless nickel coatings are particularly valued for their wear resistance and corrosion resistance. Unlike traditional electrolytic processes, electroless nickel coatings are deposited uniformly without the influence of current density distribution, resulting in consistent thickness across complex geometries.
Importance of Uniform Thickness
The uniformity of electroless nickel coatings is a significant advantage. For instance, the thickness variation in electroless nickel coatings is typically less than five percent, even in deep recess areas. This uniformity is essential for ensuring effective corrosion protection, as demonstrated by the comparative analysis of electroless and electrolytic nickel coatings.
Mechanism of Corrosion Protection
Electroless nickel coatings provide corrosion protection by encapsulating the substrate, forming a barrier layer that prevents corrosive elements from reaching the underlying material. The nickel-phosphorus layer is inert to many corrosive conditions and forms a strong oxide layer that further protects the surface.
Factors Affecting Corrosion Resistance
The effectiveness of corrosion protection is influenced by several factors:
- Surface Preparation: A defect-free substrate is critical. Inclusions from casting or fabrication processes can lead to defects in the coating.
- Coating Thickness: Thicker coatings generally provide better protection. For example, a thickness of 75 microns is recommended for extreme environments, while 20 to 30 microns is typical for automotive applications.
- Operating Parameters: Bath filtration, agitation, and the use of appropriate raw materials are essential to minimize defects during the plating process.
Evaluation Methods for Corrosion Resistance
To assess the corrosion protection of electroless nickel coatings, several testing methods are employed:
- Peroxide Test: This test reveals pores in the coating by reacting iron ions with potassium hexacyanoferrate.
- Salt Spray Tests: Various salt spray tests, including neutral, acetic acid, and copper accelerated acetic acid tests, are used to evaluate the corrosion resistance under different conditions.
- Water Climate Test: This test simulates corrosive environments by using sulfur dioxide to accelerate corrosion.
Correlation Between Thickness and Porosity
Research indicates a direct correlation between coating thickness and porosity. For instance, coatings around 30 microns thick exhibit near-zero porosity, which is crucial for effective corrosion protection. The presence of pores can lead to substrate corrosion, especially in moist environments.
New Developments in Electroless Nickel Processes
The webinar highlighted the introduction of the Nikem HP 1170 process, which offers enhanced corrosion protection through improved formulation and process parameters. Key features include:
- High Phosphorus Content: The process achieves a phosphorus content of 10 to 12 percent, enhancing corrosion resistance.
- Compressive Stress: The new process maintains compressive stress throughout the bath life, contributing to the durability of the coating.
- Environmental Compliance: The formulation is free from toxic heavy metals, aligning with environmental regulations.
Performance Comparison
In comparative tests, the Nikem HP 1170 process outperformed previous generation processes in terms of corrosion resistance. For example, panels coated with Nikem HP 1170 showed no red rust after extensive exposure in salt spray tests, demonstrating superior performance over traditional methods.
Conclusion
The advancements in high phosphorus electroless nickel coatings represent a significant leap forward in corrosion protection technology. By focusing on uniform thickness, minimizing porosity, and utilizing innovative processes like Nikem HP 1170, manufacturers can achieve enhanced durability and longevity for components in corrosive environments. As the industry continues to evolve, these developments will play a crucial role in meeting the demands of various applications, from automotive to marine environments.
Innovating for Sustainability: MKS Atotech Unveils the Future Without Hexavalent Chrome
MKS Atotech introduces innovative processes to replace hexavalent chromium in electroplating, focusing on sustainability and compliance with upcoming regulations. The webinar discusses the Coveron 600 process and Tri Chrome family, highlighting their effectiveness and compatibility with existing systems.
In a recent webinar, MKS Atotech presented groundbreaking advancements in the electroplating industry aimed at eliminating hexavalent chromium, a substance known for its harmful environmental impact. Moderated by Katarina, the session featured insights from Dr. Ernesto Zaza and Johnny Punon, both experts in the field with extensive experience in electroplating technologies.
Speakers Introduction
Dr. Ernesto Zaza
Dr. Zaza holds a PhD in chemical engineering and has over 30 years of experience in the electroplating industry. He currently serves as the Global Technology Application Manager at MKS Atotech, where he drives innovation in decorative and functional applications.
Johnny Punon
Johnny Punon, with an MBA and a background in chemistry, has 18 years of experience in the electroplating sector. He is the Business Unit General Manager for decorative coatings and has held various leadership roles across regions, focusing on business growth and market strategies.
Webinar Structure
The webinar was structured into two main parts: a 45-minute presentation followed by a 15-minute Q&A session. Attendees were encouraged to submit questions throughout the presentation, ensuring an interactive experience.
The Future Without Hexavalent Chromium
Overview of Hexavalent Chromium
Hexavalent chromium, commonly used in electroplating, poses significant health and environmental risks. The industry is under pressure to find alternatives as regulations tighten.
Coveron 600 Process
Dr. Zaza introduced the Coveron 600 process, a chrome-free etching solution for ABS and ABS/PC plastics. This process is designed to replace traditional chromic acid etching, providing similar performance while adhering to sustainability standards. Key features include:
- Temperature Efficiency: Operates at 35 degrees Celsius, reducing energy consumption and minimizing dimensional changes in parts.
- Compatibility: Works with existing plating lines and various substrates, including 2K and 3K parts.
- Performance: Meets rigorous automotive standards, passing thermal cycling tests without defects.
Tri Chrome Family
Johnny Punon discussed the Tri Chrome family, which offers alternatives for decorative chrome plating. This family includes:
- Triome Plus: A direct replacement for bright chrome, providing excellent corrosion resistance and aesthetic qualities.
- Triome I: Designed for achieving the brightest finishes, matching benchmark colors.
- Dark Finishes: A range of processes for achieving various dark chrome finishes, suitable for automotive applications.
Regulatory Landscape
The webinar highlighted the ongoing regulatory changes regarding hexavalent chromium. The authorization process for chromium trioxide is pending, with significant changes expected by 2027. MKS Atotech is committed to helping customers transition to compliant processes, emphasizing the importance of early preparation for these changes.
Sustainability Commitment
MKS Atotech's innovations not only aim to replace harmful substances but also focus on sustainability. The Coveron 600 and Tri Chrome processes are designed to eliminate both hexavalent chromium and per- and polyfluoroalkyl substances (PFAS), addressing two major environmental concerns in the industry.
Conclusion
The webinar concluded with a summary of the key points discussed, emphasizing the industrial viability of the new processes and their alignment with sustainability goals. MKS Atotech is dedicated to supporting its customers in navigating the transition to safer, more sustainable electroplating practices.
Q&A Session
The session wrapped up with a Q&A segment, where attendees posed questions about the processes, costs, and regulatory implications. MKS Atotech's experts provided insights into the practical aspects of implementing these new technologies in existing production lines.
Final Thoughts
MKS Atotech's commitment to innovation and sustainability positions it as a leader in the electroplating industry. By introducing processes that eliminate hexavalent chromium, the company is not only enhancing product quality but also contributing to a healthier environment for future generations.
For more details and purchase Atotech Products contact Email: info@essesstrading.in Mobile: 9843019701
ESS ESS TRADING inviting to Surface Coating Expo 2025
We are pleased to invite you to CII India Surface Coating Show 2025, which will take place at the Chennai Trade Centre, C...
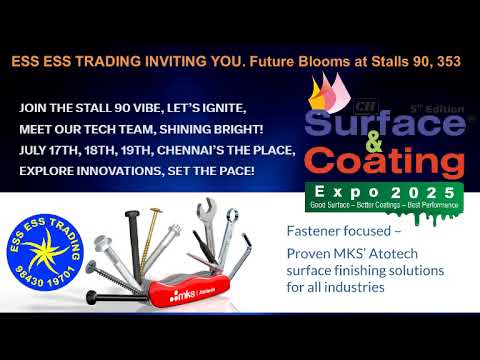
-
pic.twitter.com/jZLuEPJGFn — Ess Ess Trading (@essesstrading) December 27, 2020
-
We supply Atotech Cupracid ultra Part A, Cupracid ultra Part B, Cupracid ultra makeup, Cupracid leveller addtive and Cupracid wetting agent....
-
To buy this product at the Price Rs 350 including GST Click Here . We supply high purity electroplating grade Copper Sulphate. 99.99...